Cooling and ventilation system for CHP plant
Alara-Lukagro delivered the complete cooling and ventilation system for all the 20 Gas engines at the KIEL CHP plant. For this project we delivered and installed the louvres, dampers, pre heaters, filters, attenuators, fans, sound insulation/absorption panels, acoustical doors, acoustical bents, and the complete ducting for the engine room.
KIEL CHP Plant
The gas-engine based combined heat and power CHP plant in Kiel (Germany) supplies over 73 000 households and facilities in Kiel with district heating. Additionally, the electric power generated feeds into Kiel’s 110-kilovolt power grid, which supplies electricity both to households in the state capital and some of the surrounding municipalities. Excess energy is passed on to the upstream power grid.
Teamwork with renewable energy
The facility replaces a 323 MW coal-fired power station. Eliminating the coal-fired power plant is part of the government’s plan for a cleaner electricity sector. The new plant is designed to work in tandem with the expansion of renewable energy. When sun and wind doesn’t generates enough energy, the Jenbacher gas engines can achieve full capacity in less than five minutes.
The cooling and ventilation system
Alara-Lukagro designed and calculated all the attenuators for the air inlet (210.000 m3/h) and air outlet 160.000 m3/h, according to the cooling and acoustical demands. When all engines are running there is moving approx. 4.200.000 m3/h of air. For the air outlet we had to design special attenuators due to the fact that the exhaust pipe of the Gas engine crossing this room emitting extra noise.
Energy efficient design
With our new ventilation/cooling design we were able to optimized the energy consumption to a minimum. Therefore we made a new functional description which was implemented in the new software program. During FAT and SAT tests it was proven that this design was even better than calculated.
With the Alara-Lukagro new ventilation/cooling design we were able to optimized the energy consumption to a minimum. Therefore we made a new functional description which was implemented in the new software program. During FAT and SAT tests it was proven that this design was even better than calculated.
With our designed and manufactured attenuators, we achieved the optimum between noise control and pressure losses, what is necessary to optimize the energy consumption of the cooling fans.
Project leader on site
During the installation our project leader was continuously on site, to control that each component was installed correct and within the requested time schedule.
Control measurement
To double check that everything was working correctly, we have done flow and pressure difference measurements. We also afterwards did the acoustical control measurement. Reason to do this is that with these practical values we continuously improve our own acoustical calculation programs.
More information?
Are you facing a similar challenge?
Contact us with your questions and we will be delighted to advise you on a suitable solution for your project.
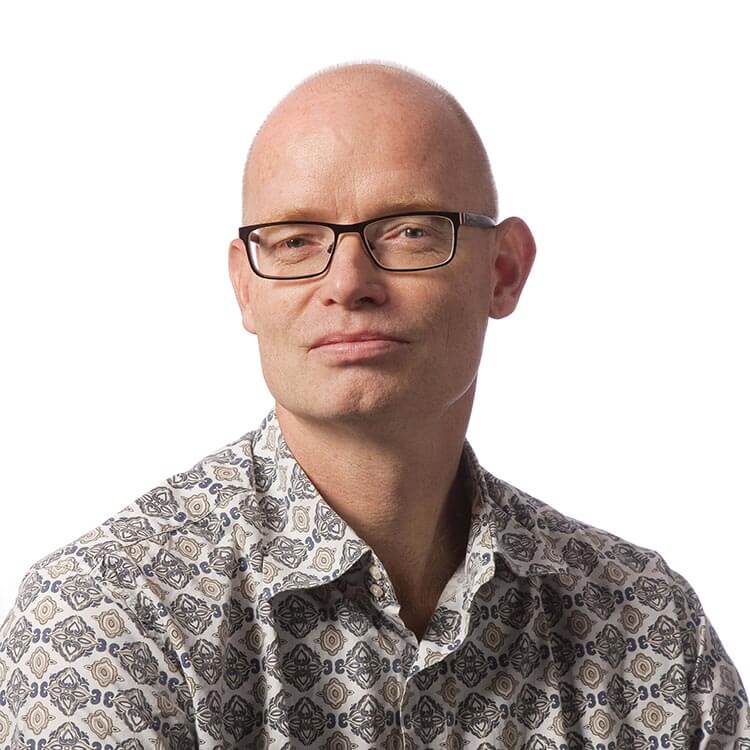